A year after Boeing’s blowout, quality remains work in progress
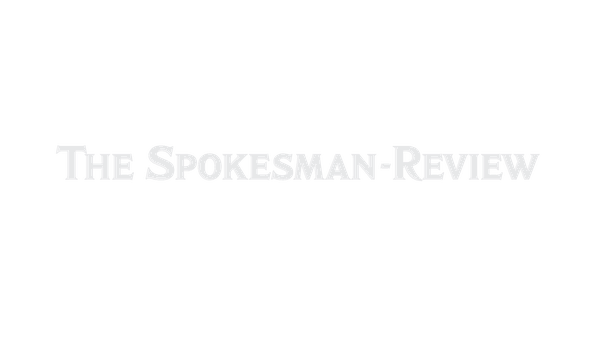
One year after a near-catastrophic accident tipped Boeing Co. into a state of continuous crisis, the top U.S. air-safety regulator cautioned that the planemaker’s efforts to improve its manufacturing quality are still in the early stages.
“This is not a one-year project,” outgoing Federal Aviation Administration Administrator Mike Whitaker said Friday in a statement. “What’s needed is a fundamental cultural shift at Boeing that’s oriented around safety and quality above profits.”
His comments suggest that it will take time before Boeing can hope to be relieved from a production cap instituted by the FAA in the wake of the Jan. 5, 2024, fuselage blowout.
The freak accident on an airborne 737 Max 9 operated by Alaska Airlines led to a year of turmoil, with regulators, airline customers and workers all lashing out at the planemaker for losing its way. Boeing was forced to raise fresh capital after financial losses kept piling up, and the company switched out senior management in bid to make a fresh start.
Boeing separately released a range of actions highlighting progress it’s made in the past year, from better teamwork and more intense training to fewer flaws in the fuselages built by a key supplier. Many of the steps listed are centered around collaboration and process improvements, highlighting how Boeing is trying to change work flows at its factories.
To ensure the planemaker is on the right track, the FAA has been meeting with Boeing weekly, holding monthly status reviews with company executives, and has increased the number of unannounced audits, Whitaker said.
Permanent change “will require sustained effort and commitment from Boeing, and unwavering scrutiny on our part,” Whitaker said, pledging that “enhanced oversight is here to stay.”
Follow-through at the FAA, however, will depend on his successor. Whitaker has announced that he plans to step down on Jan. 20 when Donald Trump assumes the U.S. presidency for a second time.
The shortcomings that forced wholesale changes at Boeing aren’t new. For the better part of six years, the company has lurched from one crisis to the next, its path strewn with catastrophes: two fatal crashes, breathtaking safety lapses and a workforce in open rebellion. Along the way, the company has racked up about $32 billion in losses.
The drama hasn’t let up since Boeing’s new Chief Executive Officer Kelly Ortberg joined the company in August as part of a management shakeup.
Ortberg, 64, came out of retirement to take the helm at the planemaker. In his short tenure, the engineering veteran has faced challenges that would faze the most battle-hardened corporate leaders – a debilitating strike in September and a cash squeeze that required a $24 billion infusion. The CEO told workers in November that his first weeks in office felt like an entire year.
The company needs to do less and do it better, managers need to gain a better hold on the operations and employees need to stop the finger-pointing and pull together if the company is to stand a chance against Airbus SE, its increasingly dominant European rival, Ortberg told staff in his first company-wide town hall meeting.
“He’s really good at envisioning the future,” said Clay Jones, who preceded Ortberg as CEO of Rockwell Collins Inc. and helped hone his management skills. “I would argue Boeing needs less of that right now because they’re trying to make it through today.”
Much rides on whether the company can demonstrate enough progress in the coming months for regulators to lift the cap on 737 production of 38 aircraft per month. The company is still pushing out planes well below the FAA-imposed limit, but that’s expected to change over the course of this year.
It’s unclear how Whitaker’s departure might impact oversight of Boeing, creating uncertainty over how and when US regulators will allow the company to speed output of aircraft that generate the bulk of its revenue.
Bloomberg Intelligence analysts George Ferguson and Melissa Balzano predicted in a Dec. 9 report that Boeing could lift aircraft deliveries by 45% to about 500 units in 2025. Deliveries tumbled in 2024 because Boeing’s factories were slowed to address quality shortfalls after the January blowout and were shut down for a two-month strike late in the year.
Tracking parts, removals
Several of the steps that Boeing laid out Friday address concerns that employees have flagged to US lawmakers, the FAA and the National Transportation Safety Board, which is investigating last year’s door plug blowout.
The company said it’s fully implemented a new system in final assembly of its 737 and 787 aircraft that tracks and secures parts during the manufacturing process to prevent loss or improper use. Whistleblowers have raised concerns about Boeing mishandling or misplacing parts, including faulty ones they’ve alleged could have ended up on planes. Boeing has disputed those claims.
The manufacturer also said it’s “significantly reduced” defects in 737 fuselages coming from supplier Spirit AeroSystems Holdings Inc., which Boeing is in the process of buying back, “by increasing inspection points at build locations and implementing customer quality approval process.”
In addition, the company is conducting random audits of instances when Boeing workers remove parts that are already in place, a process that requires documentation. Investigators discovered that the door plug from the January 2024 accident had been removed and then reinstalled without four bolts that would have kept it in place.
At a hearing in August NTSB Chair Jennifer Homendy bashed the company for “repeated problems with unauthorized removals” that were known and should have been addressed prior to the midair blowout.
Boeing’s factories and the ecosystem of smaller companies feeding in millions of parts haven’t been in sync – operating like a single, healthy organism – since at least 2018, according to current and former employees.
That was when 737 production peaked at a 52-jet monthly pace, and it’s also the last year the company out-delivered Airbus. But the stress of higher rates was already starting to fray the connections between Boeing and its suppliers. The model’s early 2019 grounding and the COVID-19 pandemic further weakened parts makers, confounding efforts by then-CEO Dave Calhoun to minimize so-called traveled work.
CEO’s early moves
Ortberg has made the symbolic move of relocating to Seattle, home to Boeing’s main manufacturing hub, and ousted the top executive for the troubled defense and space division after years of losses and embarrassing headlines. He’s also eliminating 10% of the workforce, cutting 17,000 jobs through layoffs and attrition.
The CEO, who declined to comment for this story, also pared back the use of corporate jets early on in his tenure to conserve cash after 33,000 workers went on strike, and cut loose a throng of costly consultants on retainer.
Alongside regulators, lawmakers have also signaled they don’t have any plans to let up on the company in 2025. Senator Ted Cruz, who is poised to take over the top spot on the Senate Commerce Committee now that Republicans will control both chambers of Congress, said he’s expecting representatives for Boeing to appear before the panel this year.
“There is no doubt that Boeing has faced very serious challenges in recent years, and in particular safety challenges that I think it is critical for the company to address aggressively and effectively,” he said in an interview on Capitol Hill in December.
“We’re going to continue to engage closely,” he said.