Port workers’ next demand: Stop robots from taking our jobs
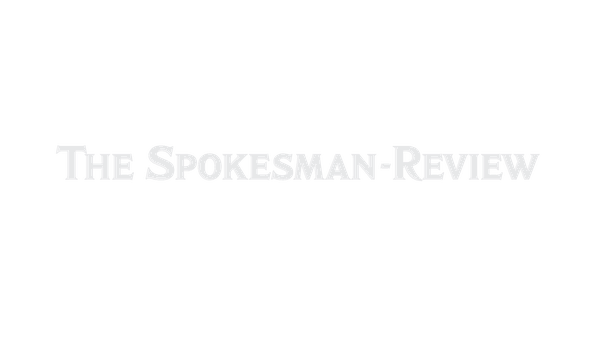
When Harold Daggett looks at the self-checkout scanner in the grocery store or the E-ZPass automatic toll lane on the highway, he does not see a modern convenience. He sees a job killer.
Daggett, the combative president of the International Longshoremen’s Association, is determined to prevent what happened to cashiers and toll booth attendants from happening to his 47,000 dockworkers. Fresh from a big win in a three-day port strike, which ended with his members getting a 62% raise over six years, the union chief will now turn his focus to a tougher foe: The march of progress.
Ports along the East and Gulf coasts reopened on Friday, after the ILA and an employers group announced the wage deal Thursday night. But the pay fight was just half of the battle. The two sides agreed to extend their previous contract, which expired Sept. 30, through Jan. 15 to allow talks to continue on the remaining issues. None looms larger than automation.
U.S. ports already lag those in Europe and Asia in their use of technology. And Daggett wants to keep it that way, by prohibiting the operators of marine terminals from automating cargo handling.
“If it was up to them, they’d like to see everybody lose their jobs. … They don’t want to pay anybody,” he said in a recent union video. “Someone has to get into Congress and say, ‘Whoa, time out.’ This world is going too fast for us. Machines got to stop. … What good is it if you’re going to put people out of work.”
The dockworkers’ challenge is not unique. Technology has been eliminating some jobs and creating others for more than two centuries. In recent decades, elevator operators, secretaries, and steelworkers all have seen demand for their services upended by mechanization.
Today, the rise of artificial intelligence has sparked fresh worries about ever more capable machines pushing humans aside.
Historically, the introduction of new technology - though disruptive - has made workers far more productive and has made the United States wealthier than other advanced nations. American workers today produce twice as much in one hour as they did in 1987, according to the Bureau of Labor Statistics.
Even as technological development has accelerated, there is no sign that more capable machines are causing permanent mass joblessness. Over the past quarter century, which included the pandemic recession, the average unemployment rate was lower than in the prior 25 years, according to data compiled by Bloomberg.
The U.S. economy has added almost 30 million new jobs over the past 25 years.
This week, Daggett demanded “absolute airtight language that there will be no automation or semiautomation” introduced during the six years covered by the union’s next contract with the United States Maritime Alliance (USMX), which represents terminal operators and ocean carriers.
The employer group offered to extend provisions in the current ILA contract, which prohibited “fully automated” equipment and gave the union an effective veto over the deployment of partially-automated systems.
“There shall be no implementation of semi-automated equipment or technology/automation until both parties agree to workforce protections and staffing levels,” the contract said.
At least two ports under ILA jurisdiction use some automated systems. In 2015, a global container terminal in Bayonne, N.J., became the first existing facility in the Western Hemisphere to field semi-automated systems. The Port of Virginia in Norfolk, which boasts semiautonomous terminal operations, bills itself as “the most modern gateway in America.”
Despite the introduction of some new technologies, the hours worked by ILA members have been growing faster than cargo volumes. Since 2019, man-hours are up 13.4% while tonnage has grown 5.1%, according to the USMX 2023 annual report.
It is not clear how the union’s existing ability to block what it regards as job-killing technologies can be enhanced. Daggett has not specified publicly the contract language he is seeking. An ILA spokesman did not respond to two requests for comment.
Daggett’s objections to automation appear genuine. In the video interview filmed a few weeks ago, he complained about the loss of union toll booth jobs and cashier positions at grocery stores and called the proliferation of cameras on the docks “Big Brother.” He reluctantly conceded that “computers” may have been a positive influence on port operations. And he has publicly vowed to take his anti-automation crusade global.
Daggett’s campaign drew support Thursday from Sen. Bernie Sanders, (D-Vt.), who posted on X: “Billionaires in the shipping industry must not be allowed to get even richer by replacing port workers with robots.”
But some analysts said the ILA may only be able to delay the inevitable.
“The argument to stop automation now is slamming the barn door decades after the horse has gotten out. This is not going to work long term. The economic incentives behind it are too strong,” said Harley Shaiken, a professor emeritus at the University of California at Berkeley, who specializes in labor issues.
The longshoremen have long resisted innovations that could displace them. When the standardized shipping container in the 1960s replaced the traditional jumble of boxes and burlap sacks that had filled cargo holds, dockworker unions on the East and West Coasts adopted different strategies, according to Marc Levinson, author of “The Box,” a history of the container trade.
On the East Coast, the ILA negotiated a guaranteed annual income that provided payments to those who could not find sufficient work on the docks. The final payments under the arrangement were made in 2005, Levinson said. The ILA’s West Coast counterpart instead negotiated a lump-sum payment in return for accepting containerization. Steady growth in trade kept the feared job losses from occurring.
“In the past, the longshore unions have agreed to various types of automation, but there’s always been some kind of price attached in terms of protecting the jobs and protecting the union’s jurisdiction,” he said. “And I assume that there is some price at which this dispute will be resolved.”
Globally, ports in recent years have introduced an array of new technologies, from automated truck gates to autonomous dock cranes that stack shipping containers and shuttle cars that move them from the quay side to the yard. The most ambitious projects require billion-dollar-plus capital investments and do not always pay off, according to a 2021 report by the International Transport Forum in Paris.
Port operators are often overly optimistic about labor cost savings, failing to recognize the need for new personnel, not all of whom may be union members, to maintain and operate the costly new equipment.
“Container terminal automation appears to offer benefits only under certain conditions and thus for a limited group of terminals,” the study concluded.
Automation makes the most sense for high-volume ports with predictable, steady cargo flows, many of which are found in other countries. In China, for example, Shanghai processed nearly 50 million containers last year, roughly six times what the Port of Los Angeles, the nation’s busiest, handled.
A relative lack of state-of-the-art systems helps explain why U.S. ports score so poorly on the World Bank’s annual ranking of trade gateways. The port of Charleston, the top-ranked U.S. facility, ranked 53rd on the 2023 list.
“Port automation is not the magic bullet that a lot of people seem to think it is. Yes, U.S. ports are comparatively inefficient when you’re looking at container lifts per hour. But there are a lot of ports around the world that have invested too heavily in automation and have found that it’s not very profitable,” Levinson said.
Fully automated ports do not yet exist. The constant, unpredictable motion of a vessel tied up at the dock requires the skills of a trained dockworker to operate the massive ship-to-shore cranes that pluck containers from the ocean carriers.
The first partially automated container terminal debuted in 1993 at the Port of Rotterdam in the Netherlands. Today, there are 53 automated terminals worldwide, accounting for just 4% of total global capacity, according to a 2021 report by the International Transport Forum.
In the United States, many ports have introduced partial automation. One industry standout is the Long Beach Container Terminal in Southern California. It handles 3.5 million standard containers annually and is the fastest facility at the Port of Long Beach, getting trucks in and out in under an hour. But another large terminal at the port, which is not automated, is often just as productive at handling containers, according to Mario Cordero, the port’s chief executive.
On the picket line outside Red Hook Terminal at the Port of Newark, strikers this week agreed that automation is their chief concern.
Lydia Ortiz, 60, said she notices each day the work that is performed by machines. No humans sitting in the toll booths, thanks to E-ZPass. Scarcely a worker to be seen at the grocery store checkout lines, filled with self-checkout machines.
“They want everything automation,” she said. “We’ve got to support families, no?”
Ortiz is approaching retirement after 25 years at the port and anticipating time with her granddaughter, who is expected later this year. But she worries about the newcomers, many of them veterans and former police officers.
“We worked in the pandemic. We work in the middle of the night. We work in the rain, we work in the heat, 24/7, 365 days in the year,” she said. “And now they want automation? How many jobs will they lose?”
Standing nearby, a burly man clad in a neon yellow safety vest, who declined to provide his name, saying that union leaders had instructed the rank-and-file not to speak to reporters, agreed.
“I don’t want to be replaced by a machine! I don’t want to fight progress, but,” he said, leaving the thought unfinished.
He shook his head and leaned into the street, displaying a sign that read: “Workers Over Machines.”