Ask the Builder: Simple concrete patching secrets
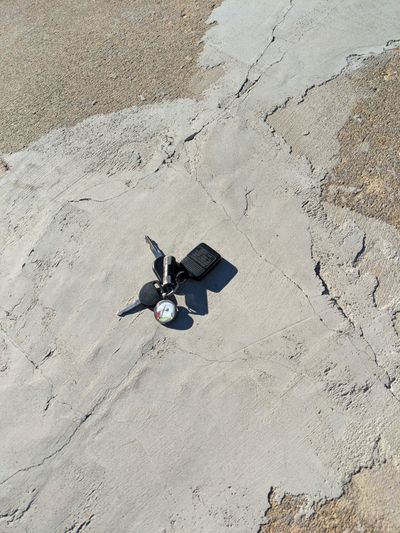
Every seven weeks, I sit in my barber’s chair and say to Mikayla: “Take no prisoners. Cut each and every one of them.” She giggles to humor me.
I have to step up from the asphalt parking lot to a concrete sidewalk to get to the shop door. Someone tried to patch a crack or a spalled area in front of the barber shop a few years ago. Spalling happens when the top surface of concrete pops off. The best analogy I can offer is peeling paint.
My eye was drawn to this botched repair job days ago. I noticed this spot was repaired at least two times. The color of each repair attempt was different.
Hairline cracks crisscrossed the most recent repair. The surface of the repair was not even. My first thought was that an amateur performed the repair. I would get the same result if I attempted to apply icing to a wedding cake. That said, if the wedding cake needed a sand and cement finish, I’d make the bride happy.
The original concrete sidewalk had a sandy finish. This promotes excellent traction, which is desired in snowy and icy New Hampshire. A sand finish on concrete works well in any climate because when it’s wet, it provides great slip resistance.
I was convinced the repair was made using a premixed concrete patching compound. These are commodity items found at any home center or hardware store. They come in small buckets. The label says they’ll work well if the area to be repaired is ¼-inch or less in depth. I have no idea how deep the hole was that was repaired.
The repair stood out like a large scar you might see on a person’s face. I grimaced peering at it. If only the person had read some of my past columns, the sidewalk would have looked so much better.
Have you ever thought about the durability of concrete? Concrete that’s been mixed, placed, finished and cured with care can last for decades. After all, it’s artificial rock. My college degree is in geology. I find it fascinating that concrete is just reconstituted rock!
Basic concrete has but four ingredients: stones or aggregate, sand, Portland cement and water.
Portland cement is made from limestone and shale. Sand, for the most part, is just tiny pieces of rock of different types and sizes. Stop and think how strong Portland cement is. Once mixed with water, a chemical reaction begins. Countless crystals start to form. They’re not unlike the hook-and-loop Velcro. The crystals bind the sand and stones together to make a hard, durable material.
Knowing this, why wouldn’t you just use inexpensive Portland cement and sand to make the repair? You already know that the cement will bond to the existing concrete.
I would have repaired the damaged concrete by making sure my repair would cover an entire block of the sidewalk. This sidewalk has tooled crack control joints every 5 feet and the sidewalk is 5 feet wide. I’d just have to cover 25 square feet with a ⅛ inch deep mixture of fine sand and Portland cement to achieve a professional repair. Fine sand can be compared to grains of table salt. It’s that small.
Let’s assume the spalled area was about ½-inch deep. I would have gathered some coarse sand to use in that deep area. The sand particles could be up to 1/8-inch in diameter. This larger sand makes the repair mix stronger in that deeper hole.
Step one of the repair process is to remove all loose and flaking material. I might tap the area with a hammer to ensure the concrete is solid. I’d then broom away all dust and even scrub it with clear water and a brush.
The weather is very important. You might think a sunny breezy day is the best time to work. It’s not. The sun and wind cause the repair compound to dry too fast. I’d want to do the repair when it was overcast and calm. An air temperature of 60 would be ideal.
I’d mix two measures of sand with one measure of Portland cement. Blend these together dry until the color is uniform. I’d then add just enough water to make the patching mix the consistency of firm applesauce.
I’d then mix up the secret ingredient, cement paint. Cement paint is made by mixing pure Portland cement with clear, cold water. Add enough water to make a mix that has the consistency of warm gravy.
If the area to be patched had dried, I’d spritz it with a water mist. It’s important not to make the concrete wet. You just want it damp. Brush on a thin layer of the magic cement paint and then immediately cover it with the sand and cement mixture.
Use a straightedge to get the patching compound even. Then wait a few minutes and swirl a magnesium or wood float over the compound to produce a professional sand finish. An hour after finishing is complete, cover the patched area with plastic and weigh it down so it can’t blow away. Keep it covered for 48 hours.
Subscribe to Tim Carter’s free newsletter at AsktheBuilder.com. Carter offers phone coaching calls if you get stuck during a DIY job. Go here: go.askthebuilder.com/coaching