Biggest auto union gears up for fight over battery worker pay
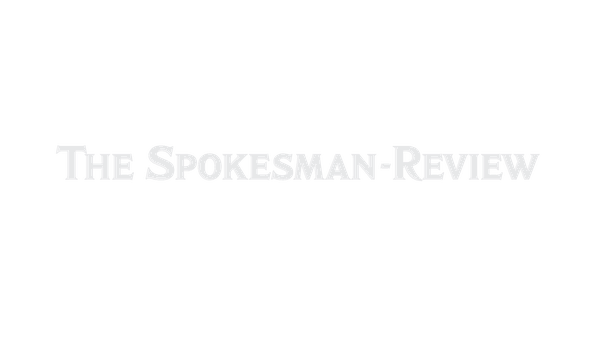
The biggest U.S. auto-industry union is preparing for a major fight with Detroit’s legacy carmakers over the future of workers at their electric-vehicle battery plants.
The dispute could be lengthy and complex, since the 18,000 or so workers those carmakers – General Motors, Ford and Stellantis – plan to hire in the U.S. will work for a patchwork of joint ventures not covered by existing labor contracts.
The new corporate structures also mean United Auto Workers, the union waging the battle over pay and benefits, might have to craft new deals for each plant.
The outcome of the negotiations, due to kick off in July and accelerate in the fall, could have far-reaching consequences – not just for autoworkers sweating the move to electrification.
As producers of everything from EV batteries to semiconductors, along with miners and processors of lithium, try to bring manufacturing back to the U.S., unions will fight to represent a new generation of workers doing jobs that moved abroad decades ago.
“The transition from internal combustion to electric has to be a just transition,” said Mike Booth, a UAW vice president who will lead talks with GM this year. “We have to make sure no one is left behind.”
One of the plants that demonstrates the complexity involved in the EV battery facility talks is the Ultium Cells plant in Lordstown, Ohio, a joint venture between GM and Korea’s LG Energy Solution.
UAW represents 1,100 workers there, but because they’re employed by the Ultium JV rather than GM directly, they aren’t covered by a master labor contract the group negotiated with GM, Ford and Stellantis four years ago.
UAW organized workers at the Ultium plant and is trying to establish a separate, first-of-its-kind deal for the employees.But even if it does, the contract won’t automatically apply to EV battery workers at other facilities without the buy-in of the automakers and their partners.
Those plants will be run by different joint ventures, so UAW has to have an organizing drive and bargain locally at each one.
Ford has plans for three battery plants with its Korean partner SK On in a joint venture called BlueOval SK, in Kentucky and Tennessee, and one with Chinese partner CATL in Michigan, starting in 2025.
Stellantis will open a plant in Indiana with Samsung SDI in 2025. GM also has three more U.S. battery plants coming with Korean partners.
UAW could secure a deal that gives Ultium workers the same pay and benefits as other GM employees, and allows union members at other facilities to transfer to the battery plant if they lose their jobs.
But the group wants to avoid creating multiple contracts. It wants to put all the battery workers under its master labor contract with GM, according to two people familiar with the group’s thinking, who spoke on the condition of anonymity because discussions are private.
GM has said the joint ventures aren’t about compensation, but about getting access to battery production and knowledge that automakers don’t have.
The company didn’t have the expertise to make batteries and needed a partner, said Gerald Johnson, GM’s executive vice president of global manufacturing.
“We needed the joint venture because we didn’t have the intellectual property,” Johnson said. As for pulling GM’s battery plants into the master agreement, he said, “that all has to be negotiated. I don’t even know if it’s legally possible.”
Labor contracts can lead to stark differences in pay. Ultium workers start at $16.50 an hour and work their way up to $22 over seven years.
Union workers who assemble cars start at $18 and work their way to $32 an hour.
The talks are all the more important because combustion-engine workers may lose their jobs as the U.S. makes the switch to electric vehicles.
“This is an existential fight,” UAW President Shawn Fain told workers in May during visit to UAW Local 1112 in Lordstown.
At the meeting, the union asked workers to sign a card pledging that they are “all in” for the fight to get battery workers a better contract.
Similar fights will play out in other industries in the coming decade.
After facing a semiconductor shortage and falling behind China and Korea on battery technology, U.S. President Joe Biden has enacted policies designed to motivate U.S. companies to reduce their reliance on other countries.
That means more workers will be needed to make semiconductors, electric-vehicle batteries and mined and processed minerals domestically – and more battles between labor unions and companies will materialize.
There is one historical example that could offer clues about how the talks between UAW and the automakers turn out.
In 1984, GM and Toyota formed a joint venture at a shuttered assembly plant in Fremont, Calif., which is now a Tesla plant.
The UAW workers there had a separate agreement from the rest of the union, but the pay and benefits were the same, according to Art Wheaton, a Cornell University labor professor.
The union could push for that in talks with each of the three auto companies this year, but can’t launch a national strike over that issue, he said.
However, they can pressure the carmaker to give battery workers the same pay and employment terms.
“Everything is up for negotiation,” Wheaton said.