Electric vehicles are reviving dead Midwestern factories
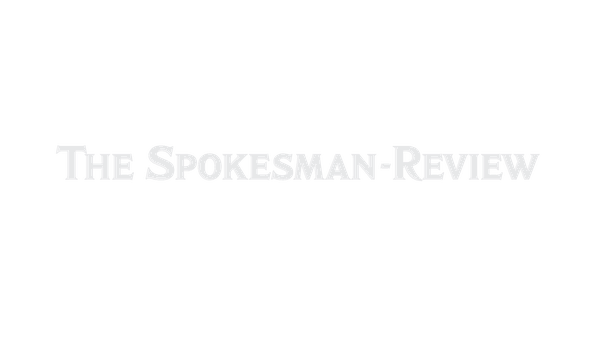
NORMAL, Ill. – When Mitsubishi closed its auto factory here in 2016, residents worried it would become another symbol of American manufacturing decline.
Six years later, the plant is back in business with a radical Silicon Valley makeover.
A fancy coffee bar and blond-wood furnishings decorate the entryway, where a wide staircase surrounded by ferns leads to the second floor.
There, engineers carrying laptops hustle along a corridor lined with glass that overlooks the humming factory floor below, a scene resembling the tidy busyness of a tech startup more than a traditional auto plant.
The factory, now owned by electric-vehicle maker Rivian, employs 6,300 people – nearly twice as many as it did under Mitsubishi – and is aiming to produce 25,000 trucks, SUVs and vans this year.
Its explosive and sometimes rocky growth will help determine how well one of the nation’s most important manufacturing sectors transitions to a new era of technology and global competition.
Ensuring that the United States makes the leap to electrification is a key goal of the Biden administration, which sees rewarding high-tech jobs and lower carbon emissions on the other side.
The White House and Congressional allies have backed the sector with new legislation that subsidizes EV purchases and charging infrastructure and incentivizes domestic manufacturing of the vehicles and batteries through tax breaks.
Many states, including Illinois, are doing the same.
The measures are accelerating a sweeping retooling of the U.S. auto industry as manufacturers modernize old factories and break ground on new ones for the electric era.
The outcome will decide which states maintain thriving manufacturing industries, and whether the United States remains one of the world’s auto powerhouses in the face of new competition from China and others.
The transition is “one of the most economically significant things happening in our region and in the country, potentially, maybe in 100 years,” Kristin Dziczek, an automotive policy adviser hired recently by the Federal Reserve Bank of Chicago to track the shift, said in a Sept. 2 interview.
“I mean, this is a really, really huge thing.”
The potential rewards for communities like Normal are clear, but there are many unknowns, including how many jobs an electrified industry creates compared with the gasoline-powered era, how quickly consumers embrace vehicles selling for an average of $66,000 and how smoothly manufacturers ramp up production.
Rivian’s mixed success in its first year of manufacturing illustrates the challenges.
It is rapidly expanding its factory and racking up orders, including a contract to build 100,000 vans for one of its biggest shareholders, Amazon.
But its production ramp-up has been slower than investors expected as Rivian struggles with component supply.
The company, headquartered in Irvine, Calif., has yet to turn a profit and was recently forced to lay off about 800 employees in nonmanufacturing positions.
The urgent drive to increase production is clear inside Rivian’s factory on the outskirts of Normal, a university town of 53,000 surrounded by some of the country’s most fertile corn and soybean farms.
On a recent afternoon, more than 50 trainees shuffled down a corridor carrying newly issued steel-toed boots, while Shawn Middlebrooks sat at a laptop nearby, trying to hire more.
To meet its production targets, Rivian is adding a second shift, for which it needs to recruit 700 to 800 people in a hurry – a difficult task amid a national labor shortage.
In the meantime, many existing employees are working mandatory overtime, which pays time-and-a-half, but risks burnout.
To speed up the hiring process, Middlebrooks and other managers are interviewing candidates in group Zoom calls.
“I think it’s really more efficient that way, honestly, because we do need a lot of people,” said Middlebrooks, a former furniture mover and small-business owner who has worked his way up at Rivian.
“It’s not like we need four people – we are hiring for a whole entire shift for every single line.”
The people who apply come from all walks of life, he said. Some are looking for their first job, while others have been in manufacturing their whole careers.
New hires get a crash course and have detailed instruction manuals to follow to learn their jobs.
“Some people have never even touched a power tool before,” Middlebrooks said. “That’s really why the [training manuals] are so important.
“You could have graduated high school, and you could have a master’s degree, and you can come in and you can read the (manuals) and interpret them in the exact same way.”
Joe Fanelli, 22, started two months ago after bagging groceries at Hy-Vee.
He earns $21 an hour on the 4 p.m. to 4 a.m. shift, using a robotic claw to move motors from a conveyor belt to a stack of pallets.
He has an undergraduate degree in digital media and said he’d like to work his way up to a more skilled role.
That would likely require more training, for which Rivian is working with nearby Heartland Community College.
Last fall, the college started an electric vehicle and energy storage program, which aims to train 360 students over the next five years.
Rivian donated vehicles and equipment to the facility, which is expanding with state funding.
Interest in the program was high enough that Heartland added a second cohort of students.
But Rick Pearce, the college’s provost, worries that factory work is still unfairly stigmatized in the eyes of young people – a concern echoed by manufacturers nationwide.
“Our community is the worldwide corporate headquarters for State Farm,” the insurance company, Pearce said.
“And so a lot of people, local kids, for instance, growing up, they look at their parents and they are white-collar workers and college graduates so they think that that is my path … and they view manufacturing as dirty.”
Rivian officials say they have tried to counter that belief by making its factory tidy and welcoming, and tying it into the engineers’ office space.
The white- and blue-collar workers share the same cafeteria, which serves hot food under a canopy of houseplants.
Artwork decorates the hallways surrounding the factory floor, and vending machines serve free sparkling water.
When Rivian bought the plant, it took the unusual step of polishing the concrete floors throughout the three-million-square-foot building, which Steve Evans, a construction coordinator who began working there as a welder for Mitsubishi, initially thought was nuts.
“I thought, why are we polishing the concrete?” he said. Later, he realized that the step “creates an environment that’s inviting. And people want to come here.”
Maintaining strong auto manufacturing in the electric era is vital for the industrial Midwest, where vehicle and parts manufacturers are bedrock employers and taxpayers.
Newer auto-manufacturing states such as Kentucky and Alabama also have a lot on the line.
“It’s a really big change in technology. It requires a whole lot of investment, and depending on where that is made, there could be important shifts in the United States in where autos are made,” said Brad Setser, an economist in the Obama and Biden administrations who is now senior fellow at the Council on Foreign Relations.
“Globally, the same is true – the regions of the world that specialize in producing internal-combustion engines won’t necessarily be the regions of the world that end up dominating the production of batteries and electric motors and exporting EVs,” he said.
General Motors this year pledged to spend $7 billion – its largest investment ever – on four Michigan manufacturing sites for battery cells and electric vehicles.
It’s also making big investments in EV and battery factories in Ohio, Tennessee, Canada and Mexico.
Ford and South Korea’s SK Innovation plan to invest $11 billion in new manufacturing campuses in Tennessee and Kentucky that will employ 11,000 people to make vehicles and batteries.
Tesla recently opened a giant factory in Austin, Texas; Stellantis and Samsung are spending $2.5 billion on a battery plant in Indiana, and Mercedes-Benz in the coming months will start producing electric SUVs at its retooled facilities in Tuscaloosa, Ala.
Illinois, a longtime manufacturer of autos and parts, has scored some early wins in the EV race by attracting Rivian and electric school-bus and truck manufacturer Lion Electric, which is setting up a factory in Joliet that could employ up to 1,400 people.
In an interview, Gov. J.B. Pritzker said Illinois is prioritizing workforce training and other support for the industry, because of the direction things are heading.
The state last year adopted a law that provides new tax credits to EV and battery manufacturers, and allows local governments to abate property taxes for such projects.
“The old Rust Belt manufacturing is going to be around for quite a while, but that is not where the significant growth is going to be,” Pritzker told the Post while attending an event last month at the Lion Electric factory.
“It’s going to be in advanced manufacturing and high-skilled labor and robotics.”
For Normal and the surrounding region, the benefits of EV manufacturing have been clear. Rivian is now the county’s second-largest employer, behind State Farm.
The manufacturer has drawn new residents from out of state, including Chief Executive R.J. Scaringe, who bought a home in the area.
That, and the rapid hiring of local employees, has sparked a boom in house prices, with Rivian employees sometimes competing for the same homes, said spokesman Zach Dietmeier.
Local hotels, restaurants and other businesses are prospering from the spillover effect.
“We have gotten booming amounts of businesses since Rivian’s started up. Whenever they get off of work, we have 10, 15 guys coming in constantly in big giant groups,” said Cierra Duzen, a waitress at The Brass Pig barbecue restaurant in the neighboring town of Bloomington.
Rivian has placed so many $2,000 catering orders that the restaurant has added a special button to its cash register, she added.
Duzen’s husband works at the factory and is currently putting in 12 hours a day, six days a week. He earns $20 an hour, with time-and-a-half for overtime and $40 an hour on Sundays, she said.In the coming months, Rivian is going to pay for him to return to school for more training, she added.
“They’ve given him every opportunity to succeed, and he’s taken advantage of that,” she said. “He loves it. He loves every second of it.”