Ask the Builder: Insulated concrete forms require extra care
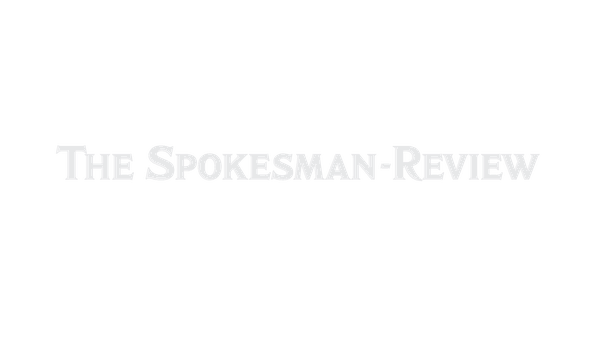
Q. Hello, Tim. I was doing research about house foundations and came across interlocking foam forms that stack on top of one another. They assemble much like children’s plastic blocks. Does a concrete foundation poured this way work as well as a traditional poured or cast concrete foundation? What, if any, are the drawbacks from using these foam forms? Is there an alternative way to achieve a well-insulated house foundation? What about the cost of an ICF foundation? –Audrey P., Mount Desert, Maine
A. Insulated concrete forms (ICF) have been around for several decades now. The industry has undergone some consolidation, but that’s normal.
I’ve seen these products at all the trade shows and I’ve been on job sites where they’ve been used. A large two-story building was built near my last home in the Midwest using ICFs. If you drove past it you’d have no idea it was a solid concrete two-story building as it was covered with lap siding.
The manufacturers typically will sing the praises of their products. Not one will readily talk about the challenges of installing them – and there can be challenges. The finished ICF foundation performs structurally as well as a traditional poured concrete foundation.
It’s important to realize the foundation footing the ICFs rest on should be perfectly flat and level. The ICF blocks are precision products and will conform to whatever they’re placed on. If the footing has humps or dips in it or is tilted side-to-side, the ICFs will telegraph all these defects. As you might imagine, it takes lots of extra time to get the footing perfect.
The footing also needs to be perfectly square so the ICFs are placed on the center of the footing with adequate flat area remaining to install any bracing that might be called for by the ICF manufacturer.
Traditional concrete forms can be aligned using special screw bracing so the walls are perfectly straight. This takes minutes to do with traditional forms, but with ICFs it might take a while longer to brace so the walls are as straight as an arrow.
Another key point is that traditional concrete foundation forms don’t require the footing to be perfectly level. The concrete poured into the forms can be made level with great ease and moderate skill using laser levels, string, finish nails and chalk. You typically pour the concrete into ICFs until it reaches the top of the last row. Thus, it’s super important that the top row of the ICFs is perfectly level. Since they stack on top of one another you can see why it’s so important for the footing to be level.
There are a number of alternative ways to achieve what ICFs do. The ICFs almost all use the same high-quality closed cell foam that you can purchase at building supply wholesalers or at the big box stores. These foam sheets can be purchased in giant 4x8 sheets that you glue to the sides of smooth poured walls. You and a helper could apply the foam to a standard foundation in a few hours using a caulk gun that dispenses an adhesive and a simple circular saw to cut the foam. The foam can be put on both sides of a typical foundation just as it will be on the finished ICF foundation.
I’d absolutely do a simple cost comparison. The cost of the concrete will be nearly identical in both scenarios. The ICFs use the same foam and you should be able to get giant sheets of foam for much less than the ICFs, but it depends on several factors.
I’ve seen traditional foundation contractors set and pour fairly complex foundations in less than eight hours. Your local ICF contractor may be able to do the same with his interlocking blocks, but as Kenny Chesney said in his hit song, “Only time will tell, but it ain’t talkin.’ ”
Subscribe to Carter’s free newsletter and listen to his new podcasts. Go to: www.AsktheBuilder.com.