Pellets with potential: Potlatch company has persevered to turn timber waste into a fuel source for sale in South Korean markets
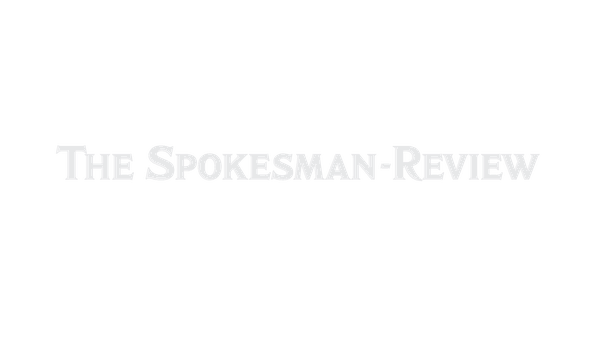
POTLATCH – A pile of seemingly neglected sawdust sitting outside a north central Idaho sawmill gave birth to Ben Anderberg’s latest big idea.
Stored outside, the sawdust didn’t appear to have much value to the mill. That made Anderberg think it could be an inexpensive raw material for another product. Four years later, he believes he’s still right.
He is a founder of Northwest Biomass, a company that began making wood pellets six months ago.
Anderberg’s eight-employee operation is taking Potlatch back to its roots in a small, but important, way.
It is the first time any manufacturing has been done in the former company town since the Potlatch sawmill closed in 1981, said Mayor David Brown.
“He took an ugly piece of ground and made it nice,” Brown said. “It’s not growing weeds anymore.”
Like Potlatch did, Northwest Biomass depends on the region’s forests. Demand for the pellets is driven in no small part by the fact that the sawdust Anderberg uses comes from trees that have been sustainably harvested. That sustainability is valued in countries with a growing awareness about climate change.

“There’s quite a market on a global scale,” he said.
Almost all of Northwest Biomass’ pellets are sold by a third party in South Korea to factories that burn them in industrial boilers.
“They get credit for burning clean fuel, and they can trade (credits) with other companies that aren’t,” Anderberg said.
Similar to his customers, Anderberg’s equipment is powered with help from wood. Undersized pellets customers would reject and wood particles unfit for pellets are fed into a furnace.
That machine that heats Douglas fir and ponderosa pine sawdust as it passes through a large cylinder along the plant’s exterior.
The heat reduces the moisture content and warms lignin, a naturally occurring polymer, in the wood, helping it act as glue to hold the pellets together and preventing the need for anything else to be added.
The sawdust is pulverized into finer pieces and compressed before being shoved through dies.
“It squeezes out like a big noodle maker,” Anderberg said. “We cut those off at about 1 inch.”
Cool air is forced through the pellets before they are dumped into bags that hold about 1 ton.
What doesn’t go to South Korea is sold in bulk. Customers who can handle 1-ton shipments can buy the pellets for $160 a ton. Equipment to put the pellets into 40-pound bags will be added later.
Reaching this stage took luck, perseverance and a willingness to learn.
Before Northwest Biomass, Anderberg was a contracted log hauler. He continues to own Big Cedar Fire Service of Kooskia, which has contracts with the state and federal government to provide firefighting equipment.
His epiphany about the potential of sawdust coincided with a visit from John Benson, a Utah friend and now partner in Northwest Biomass. Benson had money he made in the tech sector to invest.
“It was an opportunity,” Anderberg said. “The pieces kind of lined up to make it happen.”
As eager as the city of Potlatch is to have Northwest Biomass, the site posed some issues, Anderberg and Brown agreed.
“(Anderberg) went through a lot down there,” Brown said. “It was stuff none of us expected. I’m glad he stuck it out.”
The foundation of the Northwest Biomass building had to be custom designed, since a log deck from the Potlatch era sits below the ground where it was built, capped with about 3 feet of rock.
The machines Anderberg and Benson ordered from China arrived without instructions and needed more assembly than they had anticipated. Emailing the manufacturer with questions was difficult, as it wasn’t always clear if the emails were not being answered because they had been lost or were being ignored.
Lacking a background in wood pellets, they had some missteps.
At first, they thought they would use white fir sawdust because it’s readily available. Now they plan to add it to the mix in small quantities once they perfect the process more.
“It’s difficult to send through on its own,” Anderberg said.
New issues continue to surface. The rail line that takes the pellets to Longview, Wash., where they’re transferred to oceangoing ships is 400 feet from the plant. In the absence of a rail spur, Anderberg hauls each 1-ton bag to rail cars with forklifts.
“That’s a real fiasco for us right now,” he said.
Still Anderberg thinks the company is heading in the right direction. The first shipments to South Korea were accepted, and South Korean investors have visited the site and are considering helping with an expansion.