Safeguarding utility workers: UI grads create device to reduce electrocution deaths
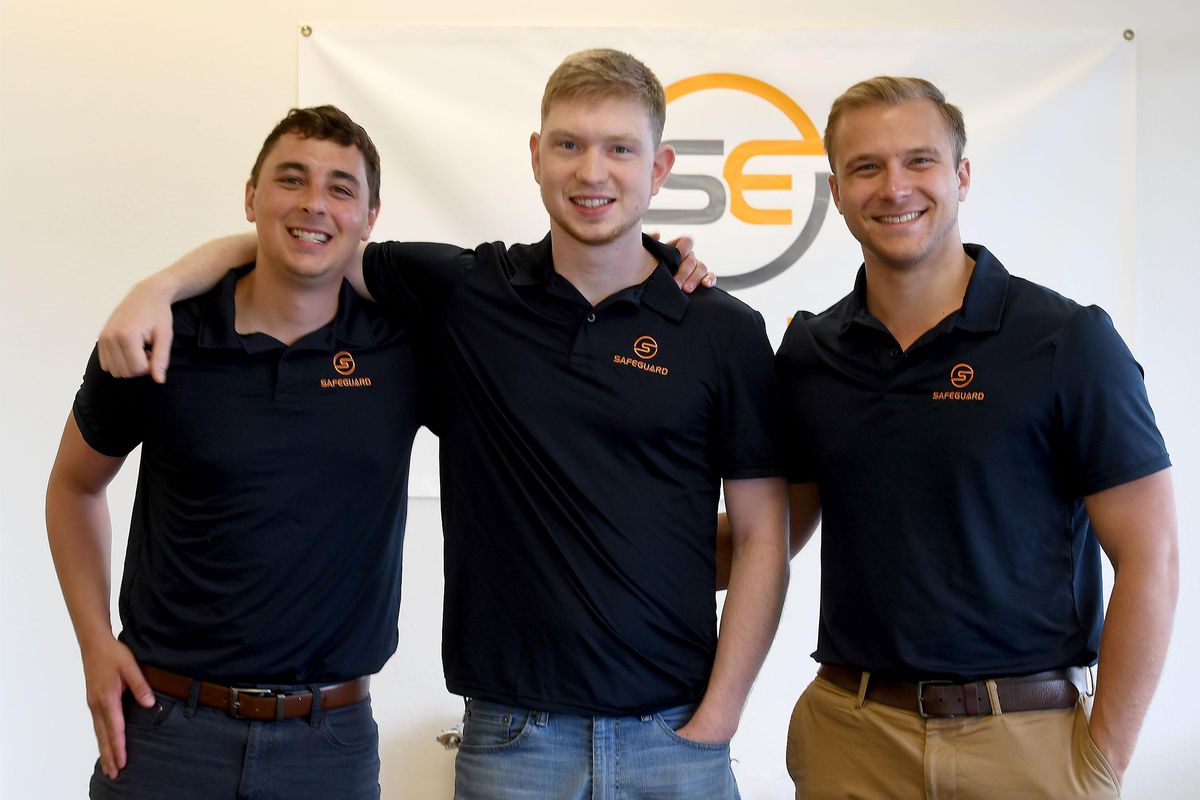
Thirty thousand dollars seemed like a fortune to the three University of Idaho graduates.
Tim Ledford, Brandon Bledsoe and John Thompson developed a safety device that utility workers clip onto their hard hats. It beeps and flashes when workers approach a high-voltage electrical source, reducing the risk of electrocution.
During their senior year, the men racked up multiple honors and $30,000 in prize money in business entrepreneur competitions. The graduates figured the money would cover the initial costs of launching their startup, Safeguard Equipment Inc.
“We were three 21-year-olds with money in the bank,” said Ledford, Safeguard’s chief executive. “We thought we could bootstrap the company.”
But getting the product to market was harder – and more costly – than they anticipated.
After graduation, they all took other jobs. Ledford put in 50-hour workweeks at Boeing while finding extra hours for Safeguard. Bledsoe designed the company’s website while moonlighting as a bartender. Thompson was in graduate school and interviewing for engineering jobs.
Seven months after they graduated, Thompson called a Skype meeting. The partners needed to devote their full-time energy to Safeguard Equipment, or give up the dream of running their own company, he said. Ledford and Bledsoe concurred.
“If we could raise some money, we agreed that we’d quit our jobs and John would quit school,” Ledford said.
The Skype meeting in January 2017 was a turning point for the young company. Shortly afterward, the Spokane Angel Alliance invited the partners to make a presentation. It awarded the company $300,000 in early stage financing, allowing the partners to quit their other jobs, file for patents and develop product prototypes.
Safeguard Equipment made its first official sale in July – there were a few small sales in late 2017, Ledford said. The company recently landed another round of investor funding from Avista Corp. and Cowles Co., the owner of The Spokesman-Review. The partners will use the seed money to scale up operations and develop additional products.
“What started out as a passion for us turned into a funded company,” Ledford said. “We realized we could make money and save people’s lives.”
Family connections
Ledford and Thompson have grandfathers, uncles, brothers and cousins who work, or previously worked, in the utility industry. Three of Thompson’s brothers are linemen. The partners knew the statistics.
Utility workers have high rates of injuries and deaths from electrocution. In 2015, 26 workers died on the job while installing or repairing power lines, according to the U.S. Bureau of Labor Statistics.
“They are the unsung heroes,” Ledford said of utility workers. “No one really talks about it outside of the industry.”
Ledford and Bledsoe, both 24, met their freshman year at their fraternity, Theta Chi. They both majored in operations management in UI’s Business and Economics Department and took classes from George Tanner, an instructor in entrepreneurship.
Until they took Tanner’s classes, they had pictured themselves working for other people after they graduated.
“He showed us that it’s viable to be an entrepreneur – that it’s OK to take risks and go for it,” Ledford said.
Thompson, 25, is an electrical engineer who brought technical skills to the table. He got the idea for the voltage and current detector from amplifier probes electricians plug into outlets to see if they are working.
“John was the Superman in this team,” Ledford said.
Ledford and Bledsoe had entered other products in business competitions, but when they started pitching the voltage and current detector, they knew they were on to something.
“People were bringing OSHA representatives over to talk to us,” Ledford said. “The industry is hungry for innovation in safety.”
Utilities’ safety officials also wanted to meet with them. “They were feeding us ideas,” Bledsoe said.
The colleagues collected advice and critiques from the business leaders judging the competitions, analyzing how they could apply the suggestions to their startup company.
“A lot of people see criticism as an attack on your idea,” said Bledsoe, but he and the others viewed it as free expert consultations. “You have to be coachable.”
Mulitple uses
The partners originally pictured a wrist-band style device. During meetings with Avista safety officials, however, they realized that wouldn’t be practical for utility workers, who wear heavy rubber gloves, or firefighters, another target audience for the product.
Avista’s feedback led to design modifications, resulting a product that clips onto the underside brim of a hardhat.
The $449 device sells under the trademark name Compass and is manufactured locally. The device uses military-grade sensors to detect the electrical or magntic fields of energized sources. Compass gives the distance and direction to the electrical source, with beeps and flashing lights that increase in magnitude as the worker gets closer.
Workers can turn off the device when they’ve identified the energized source.
Compass uses a lithium battery that can hold its charge for up to four days. During emergencies, utility employees work extended shifts, so the long battery life is important, Ledford said.
“People are getting tired and not paying as much attention” to their surroundings, he said.
Compass has applications in work settings beyond the utility industry, such as factories and firefighting, Ledford said. In Coeur d’Alene, two firefighters survived electrocution in a warehouse fire, but received serious injuries. They had stepped into a puddle, not realizing it was energized, Ledford said.
“There are other items on the market, but not as sophisticated as what they are developing,” said Steve Rector, chief financial officer for Cowles Co., who manages the company’s corporate venture fund.
“They were one of the best pitches I’ve seen,” said Mark Gustafson, Avista Development’s senior manager of business development and strategy. “They were really passionate about their invention. … One of the founders was an electrical engineer, and the CEO was a really great speaker.”
The product was compelling, too, Gustafson said. He could see a particular value for contract crews who get dispatched during storm emergencies, and utility workers who aren’t trained linemen.
Avista Development is a subsidiary of Avista Corp., using shareholder dollars to fund investment activities, Gustafson said. No money from utility customer rates is used for Avista Development’s investments, he said.
Besides offering financial support, Avista Development provided other help to the startup, including assistance with contracting and quality assurance testing, Gustafson said.
Safeguard Equipment moved into the Tedder Business Park in Post Falls in the spring. It’s the third location for the company, which started in the Toolbox in Spokane’s University District, then moved to Coeur d’Alene’s Innovation Den.
The earlier two locations allowed the partners to rub elbows with other entrepreneurs, Ledford said. They met Kevin Nichols, who became Safeguard’s chief financial officer, at the Innovation Den. Nichols has a long history of working with local startup companies.
“There are a lot startups, but very few have the product and the talent to make it happen,” Nichols said.
Safeguard has five employees, with a couple of additional hires planned. Having more workers has allowed the founders to reduce their workweeks from 90 to 60 hours.
A company’s beginning phase is challenging, because there is so much to do and learn, Ledford said. “Nothing can prepare you for it,” he said.
“You just have to be thrown in,” Bledsoe said.