Building to eliminate bouncy floors
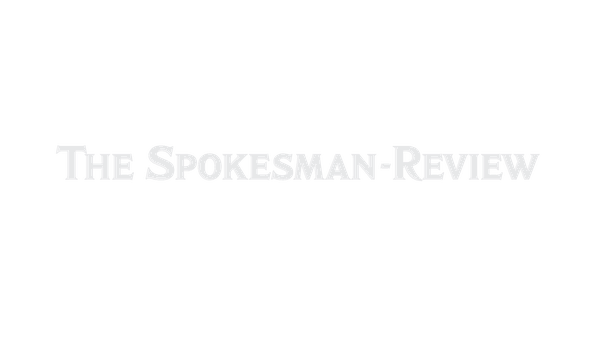
DEAR TIM: I’m in the planning stages of building a new home, and I don’t want bounce in my floors. My last home felt like a trampoline, yet it was built to code. My new home is going to have a massive kitchen with a giant island that will have a 10-foot by 5-foot solid granite top. I’m worried that the kitchen floor might sag and have bounce to it. What’s the cause of bouncy floors? How can you eliminate the bounce? I know from experience that it’s tough to solve it after the fact. – Tony M., Greenville, S.C.
DEAR TONY: Congratulations in advance on your new home. It’s always exciting to be on the verge of completing a new home. Planning is by far the most important process. Over the years, I’ve seen lots of heartache hidden in plans that were ill-conceived. I’ve also observed the inability of many to visualize what a home will look like based upon two-dimensional floor plans and elevations you see on large sheets of paper.
I’ve been in homes that had quite a bit of floor bounce. They too were also built to code, and therein lies a major problem. I think the building code is a good thing, but unfortunately most people equate a home built to code as to being one that is well built. That’s not the case. If a home is built to the code requirements, it’s about the same as you getting the lowest possible score to pass a test.
The cause of bounce is traced to the normal flex that is part of wood floor joists. Even solid steel I-beams can have flex. It’s all very complex with wood because the amount of flex varies by the species of wood and the grade of the lumber. Engineered lumber I-beams also can have flex in them, but they can be designed to be exceedingly stiff.
Some of the bounce I’m seeing in today’s new homes results, in my opinion, from builders abandoning time-tested technology. If you look at the wood-frame construction of older warehouses and homes, you’ll always see wood cross bracing in between the floor joists.
This cross bracing consisted of small 1-by-3 material that formed the letter X. The end of one of the pieces of the 1-by-3 would be nailed to the top of a joist, and the other end was nailed to the bottom of the adjacent joist.
This cross bracing helped transfer the concentrated load from one or more joists across the entire floor system. For some reason the building codes seem to have discarded this trick discovered by carpenters and builders from hundreds of years ago. It always saddens me when I see great building methods allowed to float away down the river of time.
Speaking of time, let’s go back to when I built a room addition for Matt Motz. Matt was a gentle giant and quite knowledgeable about residential construction. I was the successful bidder on a very interesting master bedroom/family room two-story addition that was to be attached to his 120-year-old farmhouse. Matt knew all about bouncy floors and insisted that his wood-frame bedroom floor be as stiff as a steel-reinforced concrete slab set on steel I-beams!
He knew the building code allowed simple 2-by-10s to span the width of the addition, but he instructed the architect to put in wood floor trusses that were 20 inches tall! My guess is this floor system had a deflection standard at least twice or three times what would pass inspection in the building code. I can tell you that the floor had absolutely no bounce in it when five or six corn-fed construction workers jumped up and down on it trying to get it to bounce.
Talk to a residential structural engineer and he or she will advise you of several possible ways to avoid floor bounce. There are many ways to achieve your goal. I happened to love working with the floor trusses because it made running plumbing, heating and electrical cables a breeze. No holes ever had to be bored because the trusses had so much open space in between the webbing.
If your wood floor system will be supported by a beam in a basement, realize that you must also pay attention to the size of the beam. Beams can be ordered and specified with different stiffness just like the wood floor joists. I always tried to convince homeowners to use taller beams for two reasons.
The taller beams not only were stiffer, but they also allowed me to create wider spacing between the columns in the basement that supported the beam. In my own home, my support columns were spaced at 16-foot intervals whereas in most homes you’d find them every 9 feet.
The money you invest with a seasoned structural engineer at this phase of the project will keep you very happy through the years. Believe me, you’ll be able to design and construct a wood floor that will be as stiff as my back after lifting 16-foot Southern yellow pine joists all day long!
Need an answer? All of Tim’s past columns are archived for free at www.AsktheBuilder.com. You can also watch hundreds of videos, download Quick Start Guides and more, all for free.