Washington apple packing getting smarter
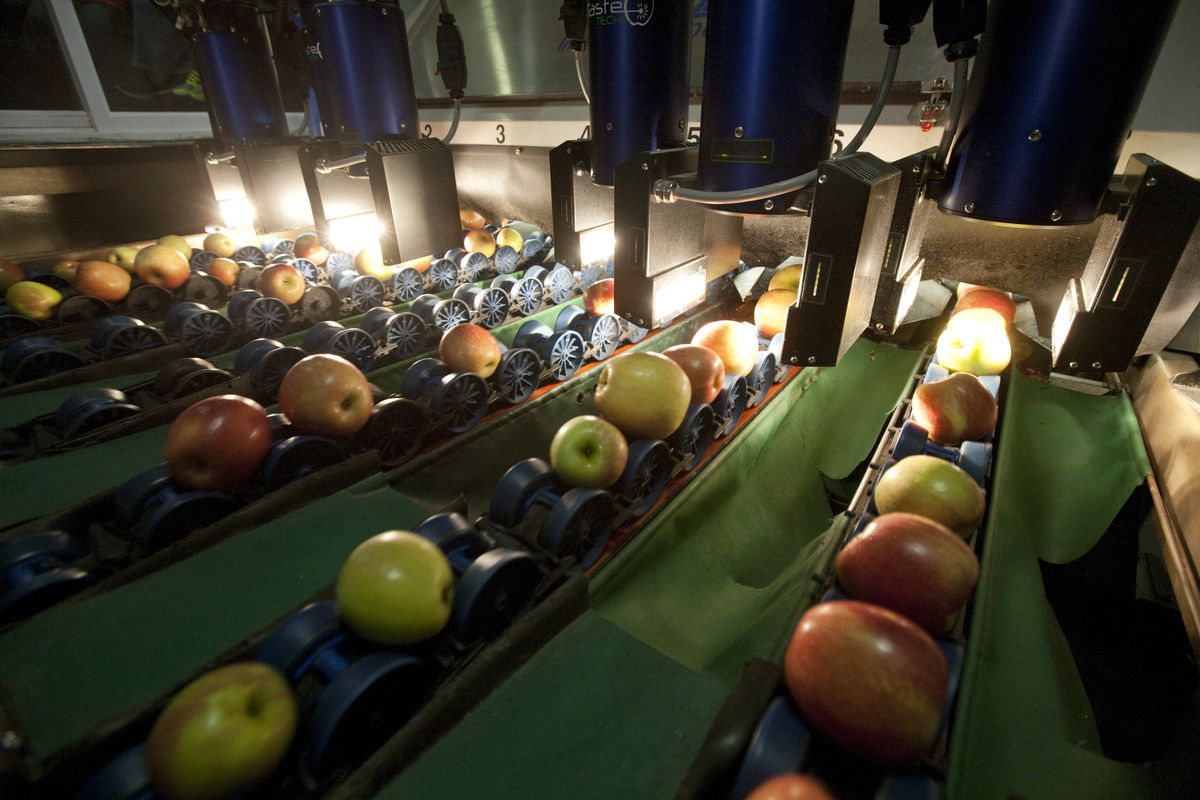
NACHES, Wash. – The job used to be done only by people with knives.
But these days on the packing line at Allan Bros. Fruit, a light spectrometer wired to near-infrared scanners checks organic Fujis for internal defects at the rate of about 2,400 apples per minute.
“If you pay $3 for an apple, it better be good,” said Miles Kohl, the executive director, justifying the millions of dollars Allan Bros. and a host of other Yakima Valley fruit packers have been spending on equipment over the past couple of years to meet the ever-rising quality demands of the global economy.
Stores around the world expect blemish-free apples. They want cherries sorted for defects, size and color with optical scanners. They don’t just want good fruit; they want computer printouts and fiber optics telling them how good.
Over a three-year span, Allan Bros. will have invested more than $7 million in packing line equipment, Kohl said.
Allan Bros. isn’t alone.
“There’s a lot of cement being poured,” said Robert Kershaw, president of Gleed-based Domex Superfresh Growers, which finished a new apple packing line roughly a year ago.
Washington Fruit in Yakima, Valicoff Fruit in Wapato and E.W. Brandt and Sons in Wapato all have similar upgrades in the works, driven by quality expectations as well as tightening food regulations and increasing labor costs.
And it helps that most packers have the money right now.
Farmers have had a run of several good years, capped by the 2012 apple harvest of a record 130 million boxes. Prices that year reached an average of $24.41 per box, also a record, as other growing regions suffered shortages.
Companies such as Washington Fruit, Frosty Packing Co. and Super Cold Storage also have plans for new controlled-atmosphere storage facilities, which decrease oxygen to slow down ripening. In 2012, area packers and storage facilities struggled at times to keep up with apple deliveries.
“It’s like everything in life: The bar just keeps getting raised higher and higher,” said Tom Hanses, packing facility supervisor for Washington Fruit. “Our customers are getting pickier and demand more.”
Washington Fruit is building a $6.7 million, 96,000-square-foot cherry packing plant on River Road and Sixth Avenue, visible from U.S. Highway 12.
That does not include the price of the equipment, which is being manufactured in Italy right now. The company hopes to have the new packing line operational by June 1, in time for this year’s crop, Hanses said.
The new line will deliver more consistent and accurate sizing, as well as boost efficiency, with an optical scanner, he said.
Valicoff Fruit Co. is installing a multimillion-dollar apple packing line at the former Inland Fruit warehouse in Wapato, which the company purchased in 2010.
Company officials hope to have it ready sometime in July, in time for this year’s apple crop.
With the new equipment, the company will be able to roughly double its capacity and still shave up to 25 employees from its workforce of 100, saving more than $500,000 a year in wages and payroll taxes, said Rob Valicoff, president of the company.
Valicoff also aims to use technology to hurdle food safety concerns, both at his plant and in the produce aisle, where people actually touch the apples, peaches and cherries.
He and his sales crews plan to focus more energy on selling bagged apples, bagging 20 to 30 percent of the crop in the coming years. His new equipment will be able to send fruit from bin to bags virtually untouched by human hands.
Valicoff also plans to build a new cold storage room as well as acquire more bins, preparing his family’s company for the future. His son Brett, 27, is getting ready to take the reins someday.
The timing is right for reinvestment after several profitable years, but upgrades are also part of the regular cost of business.
Just like smartphones are improved and updated every year, packing equipment has a shelf life of between three to five years.
For example, two years ago Allan Bros. added to one of its lines a scanner equipped with cameras that capture the entire apple’s surface area in one image, allowing it to sort for color and visible blemishes. It’s called the Compac InVision 5000, made in New Zealand.
Last August, officials purchased a new and improved version – the 9000 – for the plant’s smaller, custom pack line. It has LEDs instead of fluorescent, allowing the cameras to double their shutter speed.
In three years or so, the firm plans to replace the older model, Kohl said. By then, the packer will need a new building to house some line expansions anyway.
However, don’t expect machines to completely replace people in the packing sheds. Companies now need a new kind of technical employee to operate the computer-controlled systems.
“We have to teach it what is a good apple and what is a bad apple,” said Matt Miles, process engineer for Allan Bros. and a former aerospace engineer for Boeing. “There’s a huge learning curve and a huge investment in time.”
And off to the edge, on the opposite side of the packing line from the bank of screens, stand a few employees with paring knives, slicing into a sampling of the apples, just to check the computers’ work.
“Obviously, you can’t just look at the apple,” Kohl said.