Modular project’s goal: affordable, sustainable housing
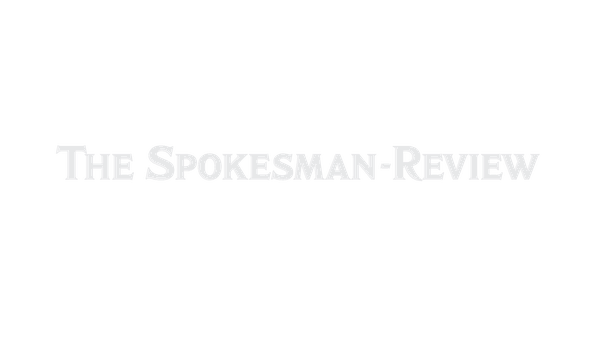
SEATTLE – Crowds gathered Tuesday to watch a house take shape as six modules were craned into place. The house is the first project by the GreenFab development team.
GreenFab is a Seattle-based developer of modular housing. The house is for Rob Humble of HyBrid Architecture, architect on the project, and will be complete in about 45 days.
Hybrid Assembly is general contractor. Site excavation began last August, and the demonstration home will be open to the public for a limited time.
The 1,790-square-foot, two-level house is made of six modules, three on each level. Modules were delivered by long-haul trucks to the Columbia City Light Rail Station, where they were staged before being trucked two miles to the site to be craned into place.
They were made by Guerdon Enterprises in a factory in Idaho. Once the modules were in place, the house was about 70 percent complete.
Using modules reduces construction time and produces less waste that typical construction. Modules also fit together tighter, forming a more efficient envelope. Factory production of modules began in early November and took two weeks.
The home will have three bedrooms, 2 3/4 baths, a 700-square-foot rooftop deck, and a flexible 400-square-foot mother-in-law space with a separate entry, kitchen and bath.
The team is targeting LEED for homes platinum and Built Green five-star certification.
GreenFab was founded in January of 2008 by longtime friends Johnny Hartsfield and Swen Grau. Hartsfield said this project has been a dream for four years. “It feels like a birth of a child, almost. This is a huge day.”
The home is targeting net-zero energy, meaning the goal is to produce all the energy it consumes in a year, and to meet the 2030 Challenge. It has a 2.4-kilowatt solar photovoltaic system, which should offset 23 percent of the projected annual electricity use. An energy recovery ventilator saves energy by transferring heat and moisture in the home that would otherwise be wasted.
Exterior walls have R 36 insulation, which is 35 percent better than code. Modules are built with advanced framing and have studs that are 24 inches apart rather than the traditional 16 inches, saving wood and increasing efficiency.
Water is another focus. All graywater from showers, bathroom sinks and the washing machine will be captured and treated. A 1,400-gallon above-ground water storage cistern will capture rainwater for irrigation and toilet flushing.
Space is provided in the backyard for a chicken coop, composting and a worm bin. Edible vegetation is incorporated into landscaping and garden boxes will be on the rooftop deck.