Biodiesel on board for trial run
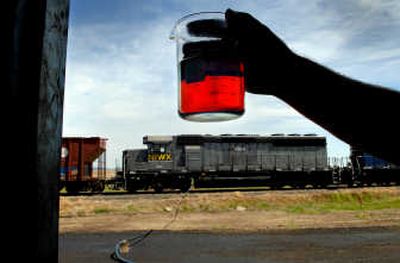
CRESTON, Wash. – When the Eastern Washington Gateway Railroad train pulled out of town Friday, it was hauling 52 cars, about 6,600 tons of wheat and – for the first time – 500 gallons of biodiesel.
It was the first leg of a journey expected to last all summer, as the railroad operator and an Eastern Washington biofuels company test whether biodiesel can work in locomotives.
The train will stop at the Columbia Bioenergy plant here every week or so for another dose of the fuel made from canola oil, restaurant grease, soy and other crops. They hope to have a good idea of how it’s working by the busy harvest time.
“It’ll continue for the summer here, and we’ll evaluate it in three months or so,” said John Howell, president of the EWGR, a company employed by the state to run the 109-mile rail line between Cheney and Coulee City.
The project is one of the first biodiesel tests on locomotives in the Northwest. So far, few trains use biodiesel, though there have been experiments in some passenger train systems in Europe and U.S. shortline railroads similar to this one – in close proximity to the crops needed and a production facility.
A 2007 article in Biodiesel Magazine reported a reluctance among some railroad operators to try something untested.
The Cheney-Coulee City line, used almost entirely for grain shipments, was purchased by the state in 2007 after years of problems.
The demonstration project arose partly from proximity – the rail line runs past Columbia Bioenergy’s plant in Creston, and the company is a customer of the railroad. John Graff, a company founder, said his plant uses regional crops to produce the fuel, so the locomotive project creates a “full loop” between the railroad and its customers.
“We’re putting fuel back into someone who is bringing us our raw feedstock and shipping our biodiesel,” he said. “I think that’s kind of a unique thing.”
Howell said the EWGR’s biodiesel test won’t save money, but he was interested in working with the customers on his route and finding ways to reduce pollution. Columbia Bioenergy, meanwhile, wants to know whether a market for biodiesel in locomotives is feasible. The railroad project comes at a time when biofuels have been under increasing scrutiny. Recent studies have shown that while biofuels may reduce emissions compared to conventional fuels, their cultivation and production make them a larger overall contributor to global warming. Also, biofuels programs and subsidies have been criticized for contributing to higher food prices by using a growing share of corn, soybeans and other crops.
Graff said that industrial uses for those crops aren’t new and biofuels aren’t the major cause of rising food prices. He also said much of the criticism aimed at biofuels is focused on ethanol, and he argued that biodiesel production is more efficient and cleaner. He and Howell emphasized that the use of biodiesel will reduce the train’s greenhouse gas emissions. “There is no question about that,” Graff said.
Graff and Brad Lyons started Columbia Bioenergy in 2005; it was the state’s first certified biodiesel refinery. Establishing the business was difficult, as interest in biofuels was rising, but the economic systems to make them work were still being created.
“It was pretty bleak,” he said. “Everything cost more money than we thought.”
The workload was so high that Graff and Lyons moved into the plant. “We had air mattresses set up in the back room,” he said. “We worked 72-hour shifts.”
Graff said the company has started to turn a profit. It produces 20,000 gallons of biodiesel a day – as well as glycerine feed from the byproduct – and supplies governments and companies throughout the Northwest that have fleets of vehicles.
“The consumer is definitely for it,” Graff said. “The petroleum industry has varying degrees of acceptance.”
On Friday, it took about an hour to pump 500 gallons of biodiesel – this batch made from canola and restaurant grease – out the back door of the plant and into the tank of the EWGR locomotive idling on the tracks. It will run a mix of about 25 percent biodiesel. Howell said engineers will be watching the fuel’s performance to see if it provides enough power or affects the engine’s operation.
“And every week or 10 days we’ll need another 500 gallons or so,” Howell said.