The problem with your sneakers? They’re built to last too long
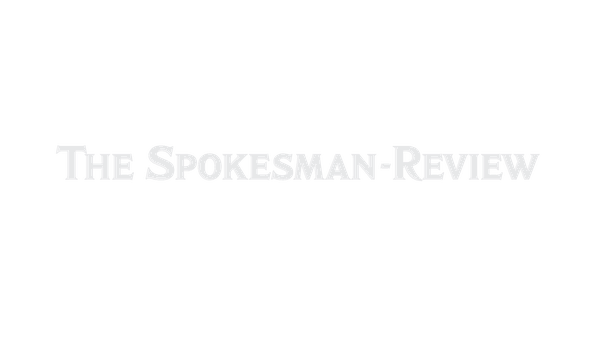
Thomas Bogle was logging dozens of miles on the spruce- and pine-lined backcountry trails that weaved around his home in Steamboat Springs, Colorado, as he trained for an ultramarathon. His mind wasn’t focused on his target pace, though. Instead, he couldn’t stop thinking about the micro bits of plastic and rubber the soles of his shoes were shedding on the forest floor.
With every step we take, our shoes leave behind an invisible trail of toxic contaminants that can potentially harm the soil, water and animal health.
Nearly 24 billion pairs of shoes were produced in 2022. Each contains myriad plastics and synthetic, petroleum-based rubber. Of the 500,000 tons of microplastics that seep into the world’s oceans each year, up to 35% come from synthetic textiles, including footwear, according to one estimate, from the International Union for Conservation of Nature.
Footwear alone accounts for 1.4% of global greenhouse gas emissions, not that far below the airline industry, which is responsible for around 2%.
Though shoe brands have taken strides toward sustainability, from offsetting carbon emissions to swapping out materials in the upper sections of shoes, they have largely overlooked soles. Now several companies are starting to focus underfoot by developing new plant-based soles that won’t leave plastics behind when they degrade.
Bogle, who spent eight years working in product development at a footwear company, is now working on an outsole from plant byproducts, while Keel Labs, a sustainable materials company started by two fashion design students, is making soles out of seaweed-based fiber. Native Shoes has a line of slip-ons made from an algae-based material, and Unless, a plant-based streetwear company in Portland rolled out a shoe made entirely of biodegradable materials in conjunction with NFW.
Shoes are designed “to last 1,000 years, and we use (them) for 100 days,” said Yuly Fuentes-Medel, program director of climate and textiles at Massachusetts Institute of Technology.
Your sneakers’ waste problem
Americans alone toss out 300 million pairs of shoes every year. According to the Environmental Protection Agency, only about 13% of clothing and footwear is recycled in the United States.
That’s partly because of the complexity of the shoemaking process. The average sneaker is composed of more than 130 individual pieces, according to Fuentes-Medel, who recently helped create the Footwear Manifesto, a report on how to make the industry more sustainable. Manufacturing a pair requires at least 100 steps on average, including stitching and gluing, she said. That makes it nearly impossible to recycle them or take them apart to reuse their materials.
The plastics in shoes also pose problems while consumers are wearing them. A 2022 study in the Journal of Hazardous Materials suggests abraded plastic from shoe soles reduces soil’s capacity to hold water and impedes photosynthesis. Another study, published in Science of the Total Environment, attributed mass coho salmon die-offs to 6PPD, a chemical added during tire manufacturing that is also found in footwear.
Plant-based soles address some of these issues. They won’t shed plastic into the environment, and making them generates fewer carbon emissions and takes fewer toxic chemicals. But shoes made with natural materials face some of the same challenges as their plastic counterparts once they’re discarded. Taking the shoes apart is still hard and recycling them will require setting up new infrastructure.
The more consumers ask for these products, Fuentes-Medel said, the more likely that infrastructure will come online, eventually leading to a more sustainable shoe industry. “You don’t want to consider your shoe something you’re going to throw away, and that’s a long-term change,” she said. “It’s a mental model that needs to change for us to keep building all the products of the future.”
A fertilizing sole
After spending more than a decade working in the industry, Bogle had an idea to create an entirely plastic-free shoe outsole – the component that was the first to wear out on his shoes during his long runs in the Colorado wilderness. He enlisted Gene Kelly, a professor of pedology (or soil science) at Colorado State University and a fellow runner, who helped develop a shoe sole made of beeswax, vegetable oils and plant byproducts such as leaves and husks from corn, hemp and other crops.
Bogle’s company, Solum, partners with farmers and producers across the country to grow and harvest the materials, before converting them into bio-pellets and blending them with natural rubber to craft the sole.
Instead of shedding toxic chemicals, Bogle explained, Solum’s soles deposit biologically derived nutrients back into the soil as they naturally wear down over time. A consumer survey by the company found that the average lifetime of a shoe outsole is around three years. Solum’s break down about 11% faster by design.
Ponto, a San Diego-based footwear brand, is planning to launch a product with a Solum outsole later this year. “Products should really be made the same way plants grow: Build it so it’s regenerative, it’s circular, otherwise our landfills are going to be filling up,” said Lanna Lottman, the company’s chief product officer. “We don’t want you to buy a shoe from us every year.”
British brand Rock Fall is releasing a number of styles that include Solum’s sole in April. The company, which focuses on safety and technical footwear, is also using algae in the upper parts of its shoes and castor oils instead of petroleum.
These days, Bogle runs and hikes, and even golfs, in shoes with his company’s plant-based soles.
“Footwear is a very hard product to fix,” he said. “It really requires completely shifting how we think about footwear and how we make footwear and the materials we use.”