Made in Spokane: Tour highlights local manufacturing companies
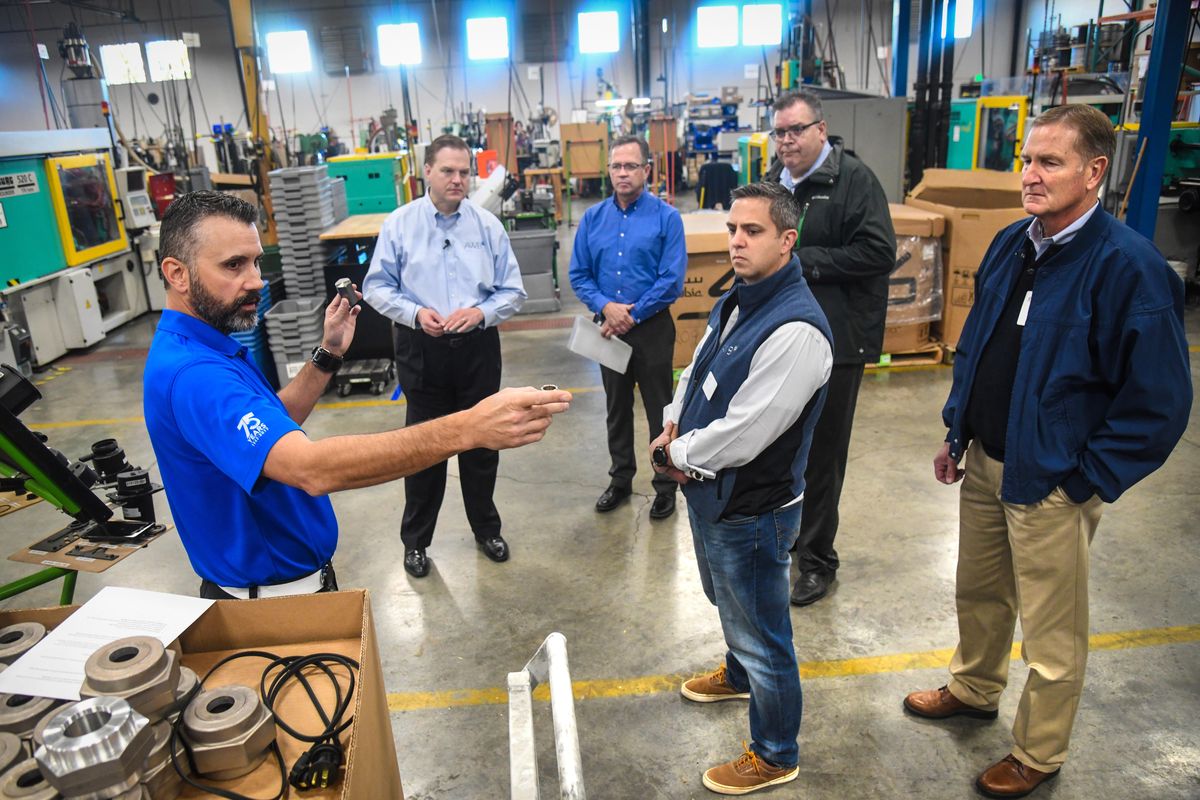
In the 1940s, a former school bus driver devised an engine heater that allowed buses to start quickly on frosty winter mornings.
Wayne Kimberlin’s invention became the genesis for Hotstart, a Spokane Valley company whose products for diesel and gas engines are sold in 180 countries.
The preheating systems keep large engines – which don’t start easily in the cold – above 100 degrees, said Terry Judge, Hotstart’s chief executive officer.
Hotstart’s products provide “a quick, clean start,” Judge said, “and they can load an engine with full power without killing it.”
That’s important for backup generators in hospitals, which must kick in within seconds of a power outage.
Hotstart was one of the companies featured on the Association of Washington Business’ Manufacturing Week bus tour, which was in Spokane County on Wednesday. The tour highlights manufacturing’s contributions to Washington’s economy with stops at about 50 companies statewide.
About 282,000 people work for Washington manufacturers, according to state figures. Spokane County has 534 manufacturing companies, employing about 15,300 people at an average wage of $53,000.
“A lot of manufacturing still takes place here in the U.S. – and Spokane – despite stories to the contrary,” said Michael Senske, chief executive officer for Pearson Packaging Systems, which also was part of Wednesday’s tour.
The tour aims to change perceptions and raise awareness of manufacturing, said Kris Johnson, AWB’s president and chief executive officer.
“People don’t realize that all this stuff is made in Spokane,” he said. “These are good jobs, tech-heavy jobs. You have an opportunity to make a difference and earn a good wage.”
Some manufacturing jobs require a high school degree and on-the-job training, Johnson said. Others can require a four-year diploma or even a master’s degree.
Hotstart growing
Officials at Hotstart and Pearson Packaging said their companies are undergoing rapid growth.
Hotstart is projecting sales of $62 million this year, Judge said. The privately owned company’s sales grew from $51 million in 2017 and $39 million in 2016.
Judge attributed Hotstart’s growth to the closure of coal-fired electric plants and increased use of cleaner natural gas as a fuel. To sustain its growth, Hotstart is looking for opportunities with electric vehicles and other areas of renewable energy, Judge said.
Hotstart currently serves various industries. Its products can show up on a backup generator for a residence, a Kenworth truck, a train locomotive or a ship, Judge said. Caterpillar Inc. is the company’s largest customer.
About 190 people work at Hotstart’s 142,000-square-foot facility in Spokane Valley, which has a “cold room” for testing equipment at temperatures as low as minus 40 degrees Fahrenheit. Another 25 people work for Hotstart around the globe.
The company has sales offices in Tokyo, Houston and the Chicago area. A new Hotstart operation in Cologne, Germany, does sales and manufacturing, targeting the marine industry.
Hotstart’s employee count has grown by about 50 over the past two years. The company likes to grow its own talent, encouraging employees to work their way up the ranks, Judge said. Hotstart offers in-house training and tuition reimbursement.
“We love to have people start with us and grow their careers with us,” he said.
Finding entry-level workers has grown more challenging. Fewer high schools offer shop classes and fewer people work on their own cars, he said.
With fewer people exposed to making or fixing things, the pool of prospective workers interested in a manufacturing career is shrinking, Judge said.
“We don’t have to have people who are highly skilled. We’ll train them,” he said. “But we want people who are motivated and excited to learn. They need to have an affinity for the work.”
Pearson Packaging
Pearson Packaging Systems designs and makes machines used by Fortune 500 companies.
The machines can open a flat, cardboard box; pack a product into the box; seal the box and stack it on a pallet. The durable machines are designed to run 16 to 24 hours per day, 365 days a year with little maintenance, said Senske, the chief executive.
Pearson Packaging just shipped about a dozen machines to a bottled water company in China. Between 20 to 25 percent of the privately held company’s sales are outside of the U.S. and Canada.
Pearson Packaging has been a presence in Spokane since 1955. It employs about 250 people at its Sunset Highway facility and about 300 worldwide. Annual sales are around $100 million.
Senske attributed robust sales to automation, with companies using machines to replace repetitive, low-skill labor. He said sales are on a trajectory to grow about 15 percent annually, not counting acquisitions, such as the February purchase of a competitor in Ashland, Virginia.
“We’re committed to growth,” Senske said. “Our large customers have demands, and we’re building to scale to meet their needs.”
To recruit talent, Pearson Packing offers regular internships to engineering students from local universities and colleges. “We don’t struggle to find labor,” Senske said.
The U.S. tariff on imported steel has been an extra cost. The price of steel has risen about 20 percent since the tariffs went into effect, Senske said. The company has added a 7.5 percent “steel surcharge” to the price of its products.
“We’re not seeing a slowdown in orders,” Senske said. “It’s more of a challenge of overcoming customers’ concerns about rising prices.”