Boeing retools plant for 737 production
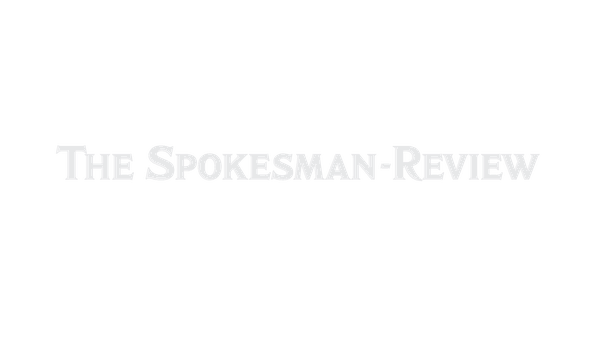
Six shiny, green 737 fuselage shells, freshly delivered by train from Wichita, Kansas, sit snugly cradled in a steel superstructure like giant eggs in a carton at Boeing’s Renton factory.
Underneath, swarming mechanics install the guts of each airplane – wads of insulation blankets, snaking bundles of electrical wiring, intricately intertwined metal hydraulic tubes and pumps.
But despite appearances, those fuselages aren’t trapped in steel.
Soon, the steel walkways encasing the jets will lift away like drawbridges, freeing the fuselages to slide 150 feet forward during the night into the next position in Boeing’s newest moving assembly line.
The factory, already a showcase of efficiency with its two final-assembly lines churning out 42 of the single-aisle jets monthly, is gearing up by 2018 to build them at a prodigious pace of 52 a month – and later perhaps even more.
A key step is extending the use of moving assembly lines to the back-end shops where mechanics build the wings and stuff those fuselage shells.
The new machinery is being installed even as Boeing choreographs the addition of a third final-assembly line at the plant. This year, that line will begin building the new 737 MAX, the next version of the best-selling single-aisle jet, which already has a backlog of more than 2,700 orders.
Director of factory operations Marty Chamberlin likens it to “changing the wheels on the car as we head down the freeway at 60 miles per hour.”
The production boom offers assurance that most of the Renton plant’s 12,000 jobs won’t go away anytime soon.
All the investment and furious re-engineering of the factory is designed, said Chamberlin, to ensure Renton remains “the most productive final-assembly plant on the planet.”
Stuffing fuselages fast
During a recent visit, big wooden crates containing 737 tail parts arriving from China were lined up along the Lake Washington shore, at the plant’s doorstep.
On the plant’s other side, a train from Wichita waited to offload its cargo of fuselage shells.
The 737 supply chain is clearly humming. The plant is rolling out two jets every workday, already a record rate of 42 per month.
Airbus pumps out its rival A320 jets at the same breakneck pace, but using three factories – in France, Germany and China.
Yet under the surface of Renton’s smooth operation, inside all is in flux.
The tightly packed area where the wiring, air ducts and hydraulics are installed in the fuselages will complete its transformation to a moving line later this year, when that egg-carton array grows from six fuselages to nine.
The fuselages are suspended on rails hidden inside this newly built fixture. Each will stay in a fixed position exactly one day, then slide to the next position that night.
On the third night, fully stuffed with all their systems, three fuselages will be lifted out by crane and swung overhead to one of the final-assembly lines.
The new process will streamline work in highly congested parts of the plane, parceling it out so crews of mechanics with distinct installation jobs don’t get in each other’s way.
And with the work divided into three physically separated chunks, mechanics can have the specific tools they need right at hand in each position, said Pat Doyle, who leads a crew working the lower fuselage.
“It’s like setting up your kitchen so you know where all the cups and plates are,” said Doyle. “It’ll clean up the flow.”
The projected new rhythm will enable Boeing to go even higher than its publicly announced production-rate goal.
Some industry analysts question the wisdom of planning to ramp up so steeply, in case market demand collapses. Yet once the new MAX assembly line is at full throttle toward the end of the decade, Renton is theoretically tooled to produce up to 63 airplanes a month.
Wings remade
In January, a barge slowly carried a mysterious, 25-foot-tall white cube through the Ballard Locks and into Lake Washington. It contained a giant Electroimpact automatic drilling machine, costing tens of millions of dollars, en route from Mukilteo to Renton.
Electroimpact’s fingerprints are everywhere in the Renton building where Boeing makes the 737 wings. The high-end engineering firm, headquartered in Mukilteo, has designed most of the automated equipment that makes the wings for both Airbus and Boeing.
Now Boeing is testing a new assembly line using the Electroimpact machines to build the 45-foot-long wing-skin panels.
Fastening the long, thin stiffeners known as stringers to each aluminum wing-skin panel requires drilling approximately 5,000 holes, or about 40,000 holes a day at current production rates of those skins.
Renton’s current drilling machines can drill and fasten 70 percent of the wing-panel holes. They cannot install bolts, which make up 10 percent of the fasteners.
Electroimpact’s moving-line system can drill 90 percent of all the holes and install bolts as well as other fasteners, completing that work in two shifts rather than the three the Gemcor machines need.
Carlos Walker, a 737 manufacturing engineer, said the new machine quietly “crushes the fastener with hydraulic force,” making much less noise than a mechanic hammering with a rivet gun.
Picking up the pace
Monthly output of 737s from Boeing’s Renton plant: 2005, 21; 2014, 42; 2017, 47; 2018, 52.
The first production wing-skin panel came off the new line in February. Sometime next year, the line will be complete with eight giant Electroimpact machines plus a spare in place, ready for a further increase in tempo to 47 planes a month in 2017.
Elsewhere in the wing facility, other Electroimpact machines automate the process of assembling the skin panels, ribs and spars into complete wings.
An automated guided vehicle glides under the semi-completed wing and lifts the lower skin panel into position. An electromagnet clamps the panel in place, and the machine drills and fastens it.
Over in one corner stands a solitary remnant of how Boeing used to assemble the wings just five years ago.
In large three-story fixtures, the 737 wing parts were held in place vertically as mechanics trudged up and down stairs from one level to the next, drilling all the holes manually.
That one lingering fixture is now used only to make the unique wings for the 737-based P-8 Navy anti-submarine jets, which are manufactured separately at a slow rate of about one per month.
It serves to remind older Renton workers of how completely their jobs have been transformed.