Growth in chips feeds Honeywell plant’s revival
Manufacturing process brings back workers
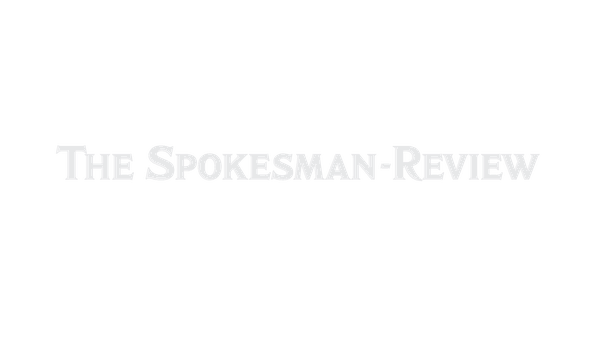
Honeywell Inc.’s Spokane Valley production plant has regained its footing, riding a resurgence in semiconductor orders to hire back workers and run some production lines 24 hours a day, company officials say.
Once one of the Valley’s largest manufacturers, Honeywell’s operation here was hit by tech downturns twice in the past decade. In its heyday in the late 1990s, the Spokane Valley site, at the corner of Euclid Avenue and Sullivan Road, had more than 600 workers.
Today its work force is at 300, up from about 270 back in 2009. Another dozen jobs are still unfilled, said Peter Dalpe, a Honeywell spokesman.
Orders are keeping the plant humming, Dalpe said. “We have some shifts that were single or double shifts before that are now 24-hour shifts.”
Honeywell is a global conglomerate with products and services across dozens of different industries, from aerospace to home thermostats. The Spokane Valley location falls into its electronic materials business group.
That sector, in particular, is riding high as tech companies worldwide are boosting orders for semiconductors and for critical components that Honeywell makes in Spokane that help in chip fabrication.
The spike in semiconductor demand is expected to push through 2011, analysts say.
Spokane’s plant doesn’t make semiconductors, but it does produce products called sputtering targets that are used by customers that bond microscopic lines or thin strips of conductive metals onto the silicon wafers.
Those metallic lines and circuits continue to be the essential way companies are able to produce faster and more efficient microchips for gadgets, computers and high-end circuit systems.
Honeywell has become one of the tech sector’s larger suppliers of targets. Spokane Valley is one of just two Honeywell plants worldwide producing those targets, a company release noted.
To meet that global semiconductor demand, Honeywell’s head office in Morristown, N.J., recently announced major investments to increase Spokane’s target production by about 90 percent.
In making semiconductors, a sputtering target is placed into a vacuum chamber, which then is bombarded with electrons. The process vaporizes some of the metal from the target and transfers that metal in microscopic patterns on the layer of the silicon chip. Those patterns become microchip circuits.
The Spokane Honeywell site is also benefiting as many semiconductor makers are moving from 200-millimeter diameter targets to 300 millimeters, Dalpe said.
The company also will double the Spokane operation’s internal production of tungsten, one of several metals used in sputtering targets. Other metals used are copper, cobalt and titanium.
Semiconductor industry analysts predict the demand for those larger wafers will increase to 4.5 billion this year, up 27.2 percent from 3.6 billion in 2009, representing the fastest-growing segment of the market.